Масштабный проект
Показательным примером воплощения как стратегии развития дорожной сети в России, так и объемов реализации заложенных проектных решений является строительство Бусиновской развязки.
О масштабности данного проекта говорят объекты, составляющие структуру будущего транспортного узла:
• магистральный участок автодороги протяженностью 1,61 км, ширина участка — до 10 полос;
• две эстакады;
• три путепровода, в том числе над путями Октябрьской железной дороги;
• шесть направленных съездов общей протяженностью 9,19 км, оснащенных 14 эстакадами общей протяженностью более 3,5 км;
• инженерные коммуникации, требующие переустройства.
Развязка войдет в состав автотрассы Москва–Санкт-Петербург до начала ее платного участка и в дальнейшем станет частью Северной рокады — хордовой автомагистрали, пересекающей Москву с востока на север, минуя центр.
Строительство развязки позволит минимизировать пересечение транспортных потоков, в том числе за счет направленных эстакад и разгонных полос, и существенно увеличить пропускную способность узла.
Для того чтобы обеспечить эффективную реализацию строительства в соответствии с утвержденными проектными решениями, на стадии инженерной подготовки объекта потребовалось выполнить масштабный вынос действующих подземных коммуникаций — освободить большую по площади территорию.
Именно об этом подготовительном этапе хотелось бы рассказать более детально. Как правило, после ввода в эксплуатацию значимых объектов вопросы, связанные с перекладкой инженерных сетей, остаются за кадром. На том, какова цена «освобождения» местности под застройку, с какими «сюрпризами» приходится сталкиваться и, наконец, какие трудности встают на пути «подземных» строителей при достижении общей цели, есть все основания остановиться подробнее. Тем более что с учетом сложившихся обстоятельств Бусиновская развязка не явилась исключением из правил.
В.Е. ГОРОВОЙ
Генеральный директор ООО "Управление инжененрных работ 701"
Связанные одной целью
Если конкретизировать задачи, которые стояли перед специалистами ООО «Управление инженерных работ 701» (ООО «УИР 701») в рамках масштабного проекта строительства транспортной развязки, то речь следует вести о перекладке подземных инженерных коммуникаций, попадающих непосредственно в зону строительной площадки. В частности, нам предстояло осуществить вынос участка действующего распределительного газопровода (рабочее давление до 1,2 МПа), проложенного и закольцованного вдоль МКАД и предназначенного, главным образом, для снабжения столичных периферийных ТЭЦ. Уже одно это обстоятельство говорит об ответственности нашего предприятия за конечный результат.
Следует упомянуть еще два важных фактора, определяющих общий уровень сложности участия ООО «УИР 701» в данном проекте:
1. Сроки строительства.
Ход и завершение выполнения работ по выносу участка трассы газопровода были неразрывно увязаны с общим графиком строительства, и любые отклонения от утвержденных сроков могли негативно повлиять на деятельность других компаний, являющихся, как и ООО «УИР 701», звеньями одной цепи в достижении общего результата. В этой связи все аспекты, касающиеся сроков выполнения отдельных этапов, жестко контролирова- лись, равно как и качество.
Бусиновская транспортная развязка в составе Северо-Восточной хорды.
Бусиновская транспортная развязка — это ключевой пункт новой магистрали Москва–Санкт-Петербург, ее по праву можно назвать Московскими воротами новой трассы. Согласно постановлению Правительства РФ (от 05.12.2001 г. No 848), реконструкция Бусиновской транспортной развязки финансируется за счет средств федерального бюджета. Реализация проекта осуществляется ГК «Автодор».
В целях перераспределения потока машин московским правительством было принято решение о продлении трассы по территории города, в связи с чем запланированы к строительству объекты:
1. Участок автодороги Москва–Санкт-Петербург (Северная рокада) — от Бусиновской развязки до Фестивальной улицы.
2. Участок автодороги Москва–Санкт-Петербург (Северная рокада) — транспортная развязка на пересечении с Фестивальной улицей.
------------------------------------------------------------
• Государственный заказчик — Департамент строительства города Москвы
• Проектная организация — ЗАО «Промос»
• Технический заказчик — ОАО «Мосинжпроект»
• Генеральная подрядная организа- ция — ОАО «Мостотрест»
• Начало строительства: январь 2013 г.
• Окончание работ: июль 2014 г.
-------------------------------------------------------------
Бусиновская транспортная развязка располагается на трассе Северо-Восточной хорды, формирование которой обеспечит осуществление транспортных связей в направлении северо-запад — юго- восток и включение системы магистралей Москвы в систему европейских транспортных коридоров, соединив скоростные автомобильные дороги Москва–Санкт- Петербург и Москва–Ногинск.
От Бусиновской транспортной развязки Северо-Восточная хорда трассируется вдоль Октябрьской железной дороги, далее на участке от Дмитровского шоссе до шоссе Энтузиастов — вдоль Малого кольца Московской железной дороги (МК МЖД), на участке от шоссе Энтузиастов до МКАД — вдоль Рязанского направления МЖД, за МКАД через районы Косино-Ухтомский, Кожухово выходит на автодорогу Москва–Нижний Новгород–Казань.
Периферийные участки магистрали являются новыми радиальными направлениями и позволят разгрузить существующие автодороги в соответствующих секторах города — Ленинградское шоссе, Рязанский проспект, шоссе Энтузиастов.
Срединный участок будет выполнять роль распределительной магистрали в соответствующей зоне города, что имеет весьма важное значение в условиях существующей радиально-кольцевой структуры мегаполиса.
Транспортно-планировочное решение Бусиновской развязки предусматривает все необходимые повороты на пересечении трех магистралей: МКАД, Северо-Восточной хорды и дублера Ленинградского шоссе, на ней строятся современные направленные съезды. В узле сохраняется всё существующее поворотное движение — с МКАД в районы Ховрино и Западное Дегунино, на улицы Дыбенко и Маршала Федоренко.
Это имеет принципиальное значение, так как на улице Дыбенко у новой проектируемой станции Замоскворецкой линии метрополитена будет создан транспортно-пересадочный узел (ТПУ) с перехватывающим паркингом, устройством удобных перронов посадки-высадки пассажиров маршрутов наземного пассажирского транспорта, как московских, так и областных.
Данный ТПУ входит в единый транспортный кластер, включающий в себя такие узлы у действующих станций метро: «Водный стадион», «Речной вокзал» и строящихся станций: «Беломорская улица», «Улица Дыбенко» московского метрополитена.
2. Плотность застройки.
Одновременное возведение на одной, хоть и масштабной, строительной площадке большого количества объектов при необходимости поддержания дорожного движения на МКАД создавало в инженерном плане крайне стесненные условия для выполнения работ. Необходимо было использовать в буквальном смысле каждый сантиметр выделенной площади.
Нельзя сказать, что участие в крупных инфраструктурных проектах с такой плотностью работ и ответственностью за конечный результат было откровением для наших специалистов. За многолетнюю деятельность предприятия аналогичных по сложности проектов было выполнено немало, что стало, можно сказать, визитной карточкой компании. Однако должной концентрации, умения работать в команде и готовности в случае необходимости предложить неординарные решения никто не отменял. И подход к реализации проекта, и общий настрой были соответствующими.
Трасса нового, выносимого из зоны производства работ при возведении объектов Бусиновской развязки, участка газопровода включала пять неравнозначных по длине интервалов: три прокола длиной порядка 50–60 м, еще два — 110 и 156 м соответственно.
техника
Буровая установка Perforator PBA-320
Perforator PBA-320 — самая мощная серийная установка. Предназначена для выполнения высокоточной бестраншейной прокладки стальных футляров методом горизонтального шнекового бурения диаметром от 325 до 820 мм на длину до 100 м, ø1020 мм - до 80м, ø1220 мм - до 70 м, ø1420 мм — до 60 м, ø1620 мм — до 50 м, ø 1720 мм — до 40 м. Установка, оснащенная дополнительным оборудованием, позволяет производить работы по прокладке полиэтиленовых (ПНД) и чугунных (ВЧШГ) труб методом горизонтального направленного бурения.
С помощью прессовой буровой установки PBA-320, укомплектованной полыми шнеками, возможна прокладка футляров без приемного котлована (так называемая прокладка вглухую). Отклонение от заданного направления при проведении работ не превышает 30 мм. Оборудование позволяет добиться абсолютно точной и прямолинейной прокладки трубопровода без провисов рабочей трубы.
Технические характеристики
Прессовое усилие — 3200 кН
Обратное усилие — 2300 кН
Шаг прессования — 500 мм
Крутящий момент — 100 кН • м
Максимальная скорость вращения — 22 об./мин.
Вес установки — 8200 кг
Максимальный диаметр трубы — 1720 мм
Минимальные размеры котлована — 9,0 × 4,0 м
Расстояние от котлована до осибурения — 1200 мм
Гидроагрегат HS-190
техника
Буровой комплекс Herrenknecht AVN800
Представляет собой мощную универсальную машину для микротоннелирования во всех категориях грунтов, вплоть до скальных. Суть данного метода заключается в том, что прокладка труб в грунте производится проходческим микрощитом. Его поступательные движения обеспечивает мощная домкратная станция, передающая толкающее усилие к щиту через колонну стальных или железобетонных труб, которая наращивается по мере продвижения вперед.
Важной особенностью технологии является высокая точность проходки и постоянный контроль траектории. При прокладке под землей коллекторов большого диаметра отклонение составляет всего несколько сантиметров.
Технические характеристики
Основная информация
Длина прокладки — 150 м
Диаметр гидропривода — 100 мм
Составной щит
Внешний диаметр щита — 1110/1295 (доп. комплект) мм
Внешний диаметр трубы — 1090/1280 мм
Внутренний диаметр трубы — 800/1000 мм
Главный привод
Максимальный крутящий момент — 90 кН • м
Вращение влево/вправо — 0–7,1 об./мин.
Номинальная мощность — 75 кВт
Коррекция вращения — Есть
Рулевое управление
Цилиндры рулевого управления — 3 шт.
Сила на цилиндр/давление — 393/50 кН/МПа
Ход цилиндра — 50 мм
Управление
Система компьютерной регистрации данных — есть
Автоматическое управление — опционально
Полное визуальное управление процессом — есть
Активная защита вращения — есть
Речь идет о прокладке футляра (стальная труба диаметром 1020 мм) с последующей затяжкой рабочей трубы (стальная диаметром 820 мм). Глубина заложения трассы варьировалась на ее отдельных участках от 4 до 18 м, что в условиях многоуровневой автодорожной развязки выглядит вполне объяснимо. Выбор технического решения выполнения проколов, осуществленный накануне с учетом оптимизации технико-экономических показателей (скорости проходки и стоимости выполнения работ), был достаточно предсказуем:
• три прокола протяженностью 50–60 м было решено производить с помощью установки шнекового горизонтального бурения Perfоrator РВА-320;
• для выполнения работ на самом протяженном интервале был выбран метод микротоннелирования с применением бурового комплекса Herrenknecht AVN800.
Грунтовые условия полосы прохождения трассы были представлены в основном суглинками, глинами и супесями. Ожидаемый водоприток квалифицировался как «незначительный». Здесь вполне очевиден скептический вопрос со стороны большого числа специалистов: «Если не брать во внимание значимость предстоящих работ и ответственность за результат, что сложного, интересного представляет проходка данных интервалов?». С этим трудно не согласиться. На первый взгляд всё выглядит достаточно обычно. Однако мы не стали бы говорить о данном проекте, если бы не упомянутые выше «сюрпризы», с которыми нам всё же пришлось столкнуться.
Первый сюрприз
Начнем с инцидента, произошедшего при прохождении самого протяженного интервала. В начале проходки — на расстоянии около 20 м от стартового котлована — возникла нештатная ситуация. Микрощит уперся в препятствие, которое оказалось для него непреодолимым. То, что удалось установить визуально, давало возможность сделать вывод о техногенном происхождении преграды и ее значительных габаритах, многократно превышающих площадь режущего органа микрощита. В такой ситуации продолжать попытки преодоления «не до конца опознанного объекта» было небезопасно. Принятое на месте решение заключалось в необходимости проходки штольни, которая позволила бы, во-первых, тщательно изучить подземный объект, во-вторых, выбрать способ устранения возникшей проблемы. Микрощит был временно извлечен на поверхность (тем более что пройти удалось совсем немного), после чего стартовали проходческие работы. Вначале по контуру будущей штольни был выстроен экран из труб (сталь, диаметр 325 мм) на расстояние от котлована до места пересечения трассы с препятствием. Для забивания стальных труб использовали пневмопробойник. Разработка и транспортировка грунта на поверхность велась внутри защищенного контура соответственно миниэкскаватором и минипогрузчиком. Штольню укрепили поперечными двутавровыми рамами, основание выстелили плитами. Сооружение штольни позволило выяснить, что путь микрощиту преграждала брошенная теплотрасса — две изолированные трубы диаметром 1020 мм в железобетонном коллекторе. Наличие свободного пространства в забое штольни дало возможность разобрать препятствие, после чего прокладка футляра методом микротоннелирования продолжилась Мы сознательно не приводим всех подробностей решения проблемы первого «сюрприза». Самое «интересное», к большому сожалению, нас ждало впереди.
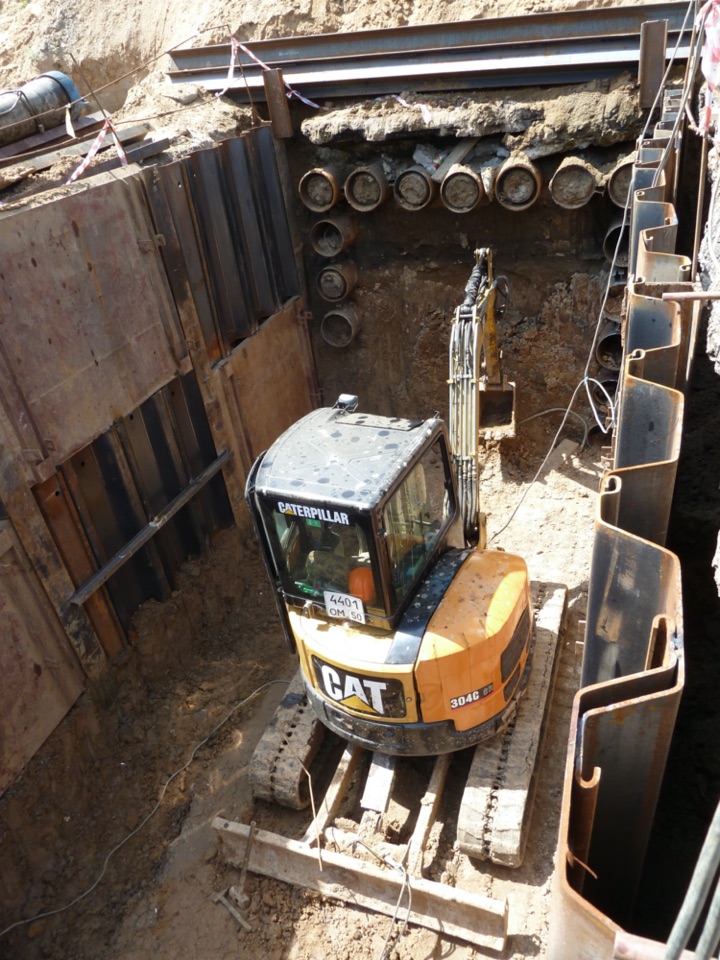
Разработка штольни
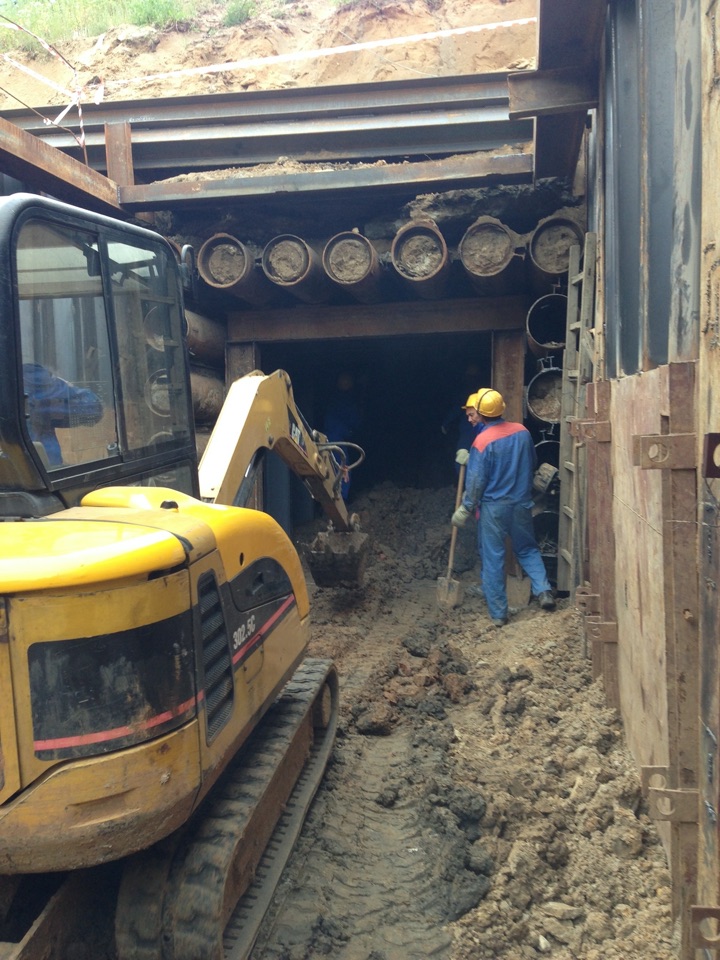
Разработка штольни
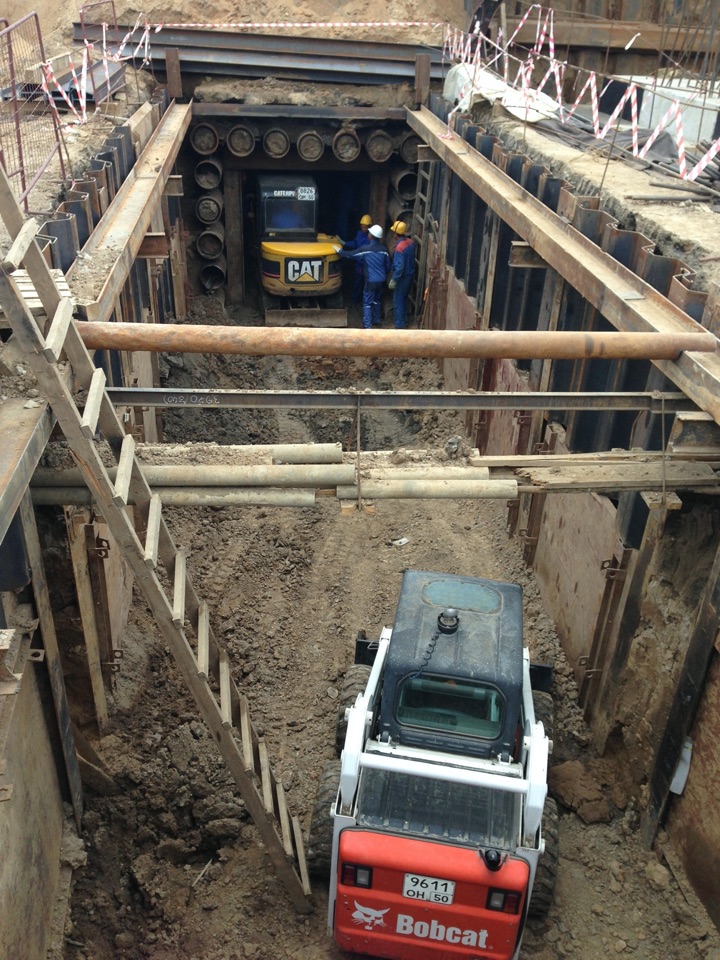
Разработка штольни
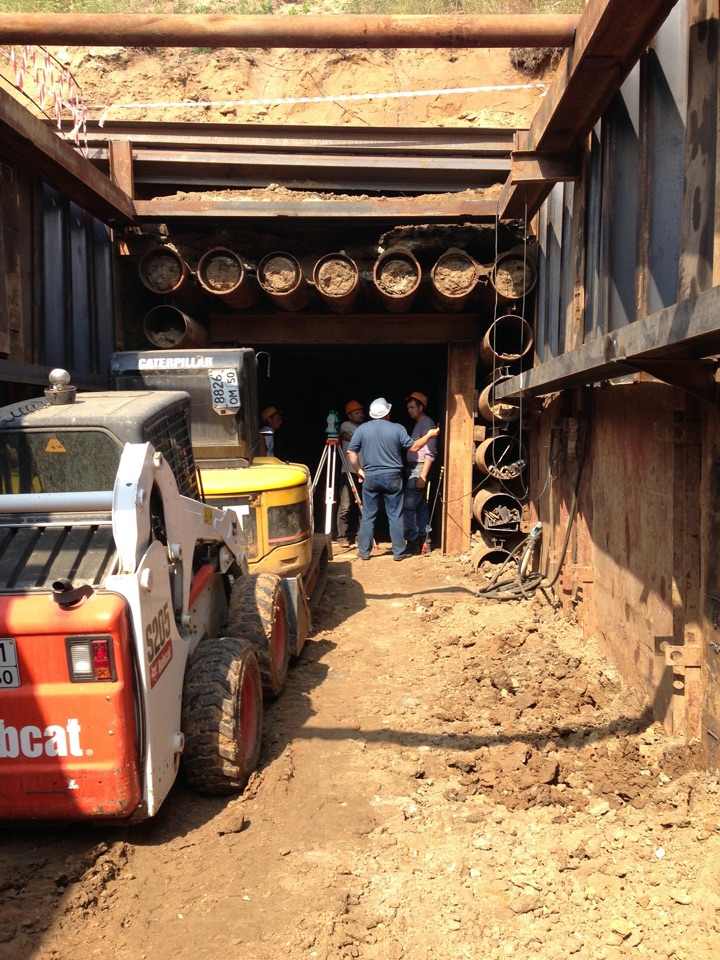
Исследование штольни
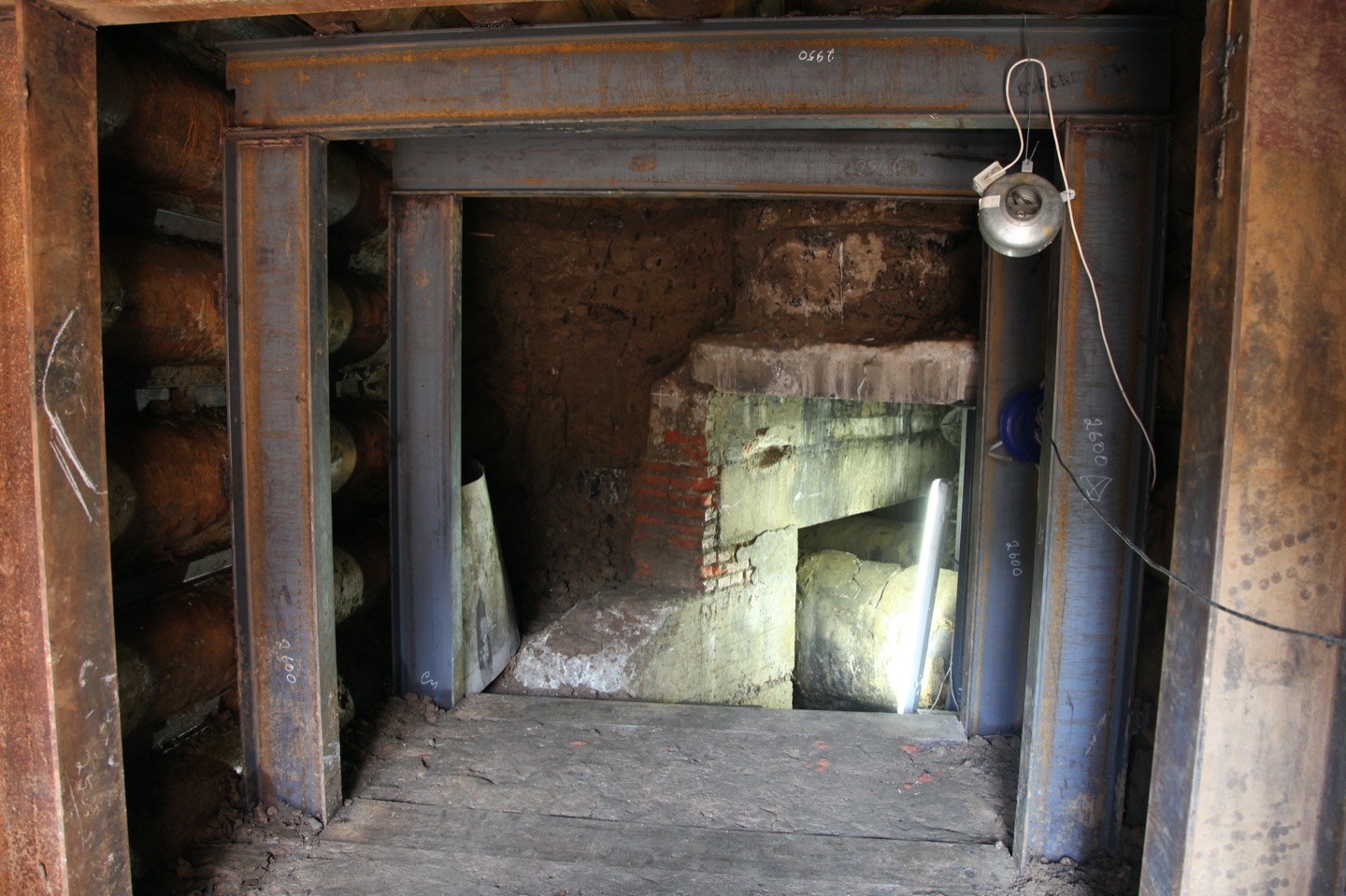
Исследование штольни
Бусиновский «шлагбаум»
Примерно до середины трассы проходка велась в штатном режиме и не предвещала каких-либо осложнений. Но вскоре появились все признаки новой помехи на пути микрощита: разработка забоя и продвижение вперед стали возможными только в случае приложения значительных усилий на продавливающей раме. Кроме того, микрощит неуклонно «тащило» в сторону. Дальнейшие попытки управлять процессом успехом не увенчались: пройти препятствие не удавалось, а ситуация в плане навигации изменилась с точностью до наоборот: теперь направление перемещения микрощита по сути задавало препятствие, а не оператор. И самое неприятное — изгиб трубопровода в месте, непосредственно примыкающем к хвостовой части микрощита, превысил максимально допустимое значение для рабочей трубы газопровода. Остановка проходки стала неизбежной. И, похоже, надолго. Необходимо было принимать принципиальное решение. Первое, что пришло в голову — попробовать обойти преграду: «уйти» в сторону или «нырнуть» вниз. Однако такого рода предложения были на корню отвергнуты проектировщиками: «Все технические изменения и дополнения должны быть осуществлены в рамках выделенного действующего технологического коридора». Откровенно говоря, такой вердикт не стал для нас большой неожиданностью. Возможности «ухода» в сторону в условиях такой плотной застройки не было по определению, а углубление трассы могло привести к дополнительным трудозатратам и росту стоимости выполнения работ. Здесь также необходимо учитывать вероятность ухудшения горно-геологических условий при прокладке новой трассы. Вариант непосредственного преодоления препятствия без изменения проекта оказался безальтернативным. Перед тем как выбрать подходящее технологическое решение из имеющихся средств и известных способов проходки, необходимо было получить четкое представление о подземном «шлагбауме», оказавшемся на нашем пути. Изучение размеров и структуры препятствия начали «с поверхности». Ознакомившись с архивной документацией и узнав мнения специалистов со стажем, удалось выяснить, что ориентировочно на месте нашего незримого «коллапса» на поверхности в свое время располагалось здание авторемонтной мастерской. Строение снесли, а вот его подземная часть, включая подвальные помещения и фундамент, скорее всего, была просто засыпана. В дополнение многие из опрошенных не исключали возможности наличия брошенных подземных коммуникаций в данном районе. Но это были лишь общие предположения. Конкретного представления о габаритах преграды и ее особенностях никто толком не знал. Стало понятным, что пройти сквозь подземное основание здания получится только путем разрушения его частей, попадающих непосредственно в забой. Выполнить это возможно исключительно находясь в непосредственном контакте с препятствием, то есть вручную. При этом мы отдавали себе отчет в том, что трудоемкость проходческих работ вырастет значительно, а темпы упадут соответственно. Но другого пути у нас не было. Технология микротоннелирования оказалась несостоятельной ввиду целого ряда объективных причин.
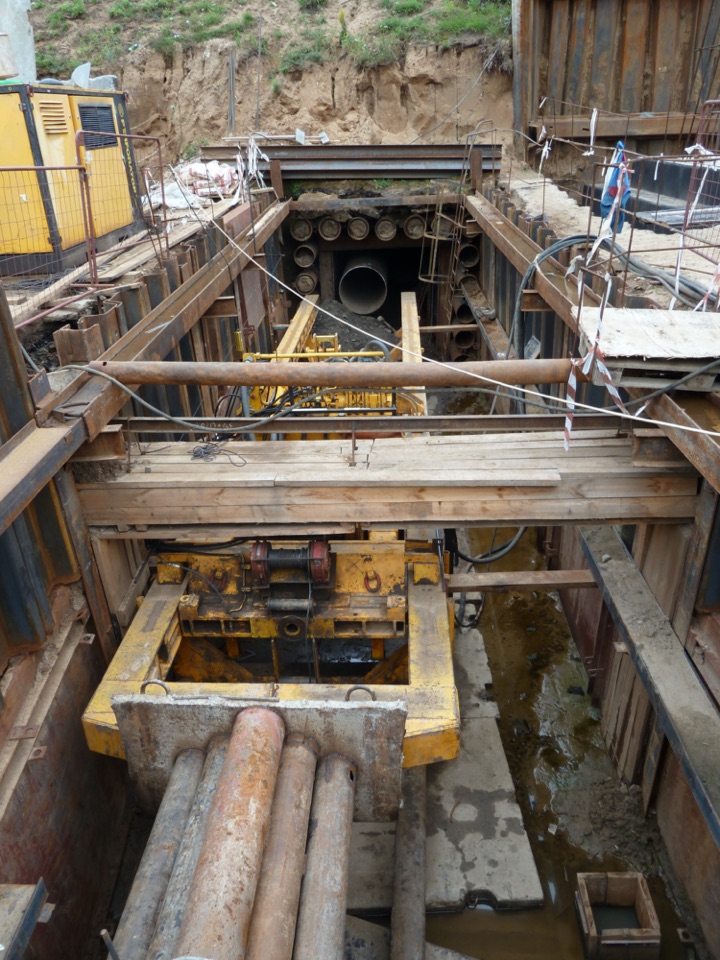
Продолжение проходки
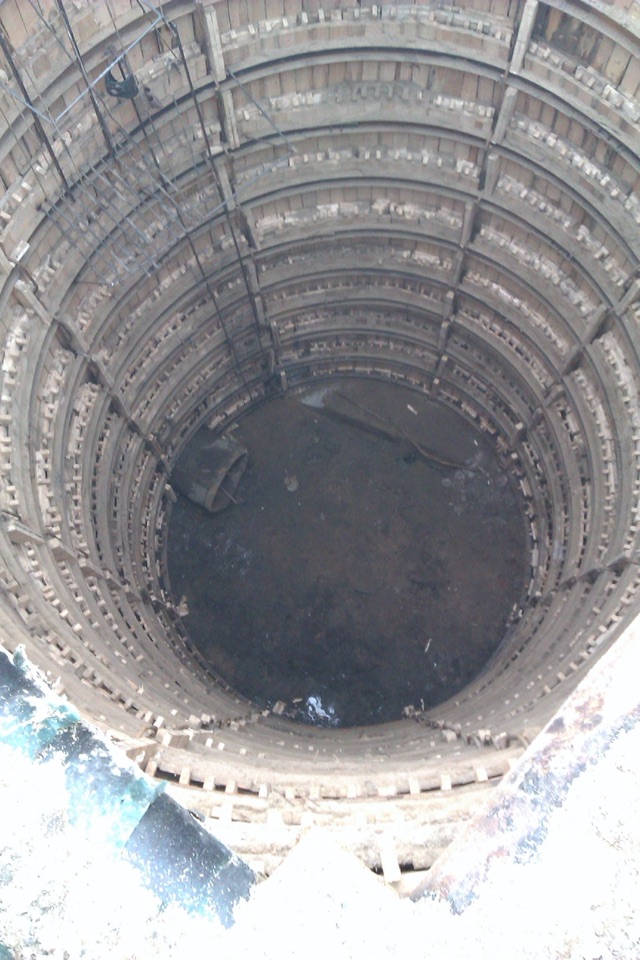
Промежуточная шахта
Принятое окончательное комплексное решение было направлено на устранение образовавшегося брака (деформированный участок футляра длиной порядка 15 м) и обеспечение возможности безопасного завершения работ на всей протяженности оставшейся части данного интервала. На практике были выполнены следующие мероприятия. В месте остановки микрощита с поверхности пройдена шахта диаметром 6,5 м и глубиной 19,5 м таким образом, чтобы расстояние от режущего органа микрощита до внешней поверхности крепежного кольца было минимальным (0,3 м). Шахта была буквально «посажена» на оставшийся в грунте фундамент бывшего авторемонтного предприятия для последующей его разборки до заданной отметки. Далее, после подготовки основания в направлении стартового котлована была пройдена штольня на расстояние 15 м, что позволило беспрепятственно вытолкнуть деформированный участок футляра и демонтировать микрощит. Эти действия дали нам возможность убедиться в том, что на участке длиной около 120 м от стартового котлована футляр гарантированно отвечал всем предъявляемым требованиям к качеству. Оставалось пройти самый сложный участок протяженностью порядка 50 м от шахты до приемного котлована. Здесь единственно надежным и безопасным решением оказалась проверенная годами технология продавливания труб. В приемном котловане была установлена машина Perfоrator РВА-320, диаметр трубы футляра увеличен до 1420 мм. Вне всякого сомнения, в условиях неизбежности проходки сквозь фундамент здания речь можно было вести только о разработке забоя с помощью отбойных молотков. И тут фортуна нам не благоволила: «борьбу» с фундаментом и подвальными помещениями пришлось начать, по сути, сразу после того, как футляр покинул пределы котлована. Иными словами, «идти в бетоне» пришлось все 50 м до выхода в шахту. Эта работа, без преувеличения, была изнурительной и неблагодарной.
К концу смены все буквально валились с ног. Сегодня, когда трудности, сопровождавшие нас в Бусиново, остались позади, и удалось немного отдохнуть и успокоиться, можно с улыбкой вспоминать, как вперемежку с кирпичом и бетоном на поверхность извлекались автопокрышки и даже станина токарного станка, забытая в подвалах здания бывшими владельцами. А тогда — в ходе проходки — всё это сильно раздражало!
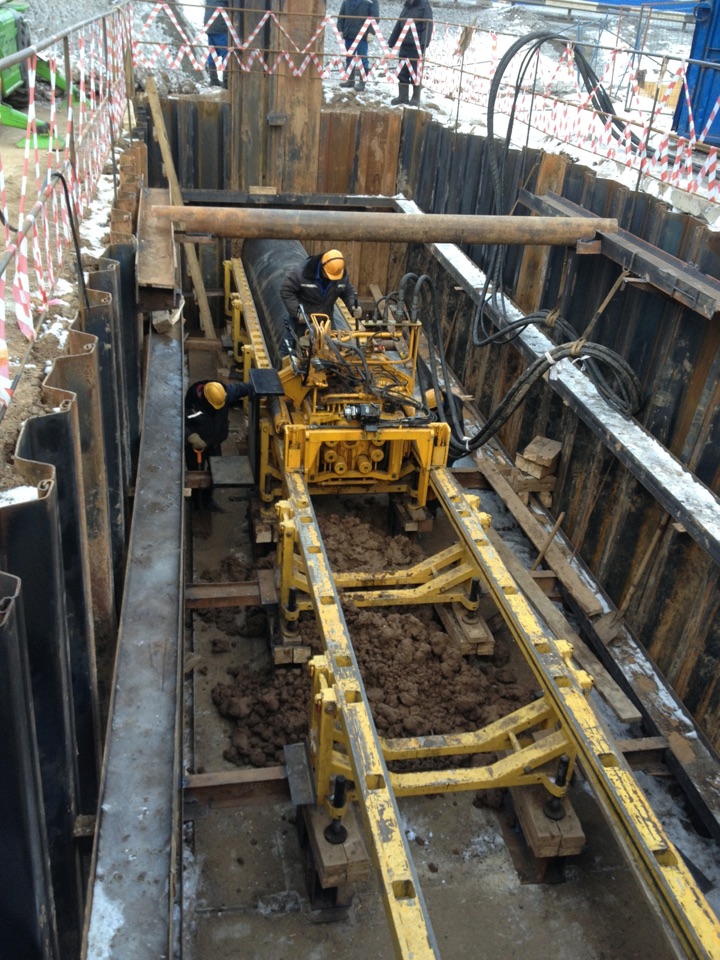
Приемный котлован
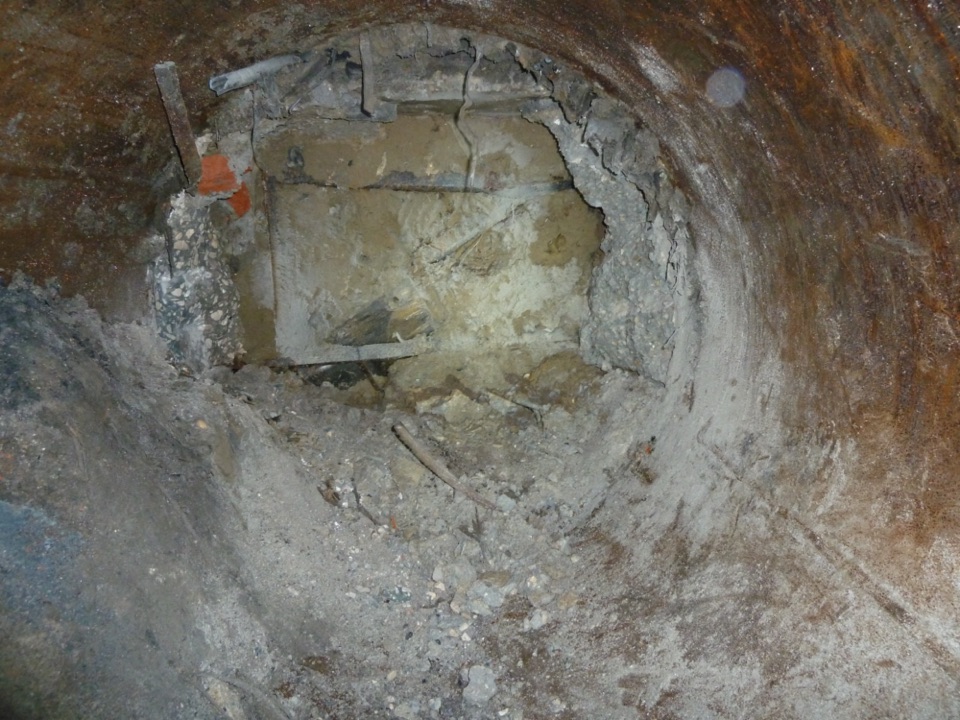
«Борьба» с фундаментом
авторемонтной мастерской
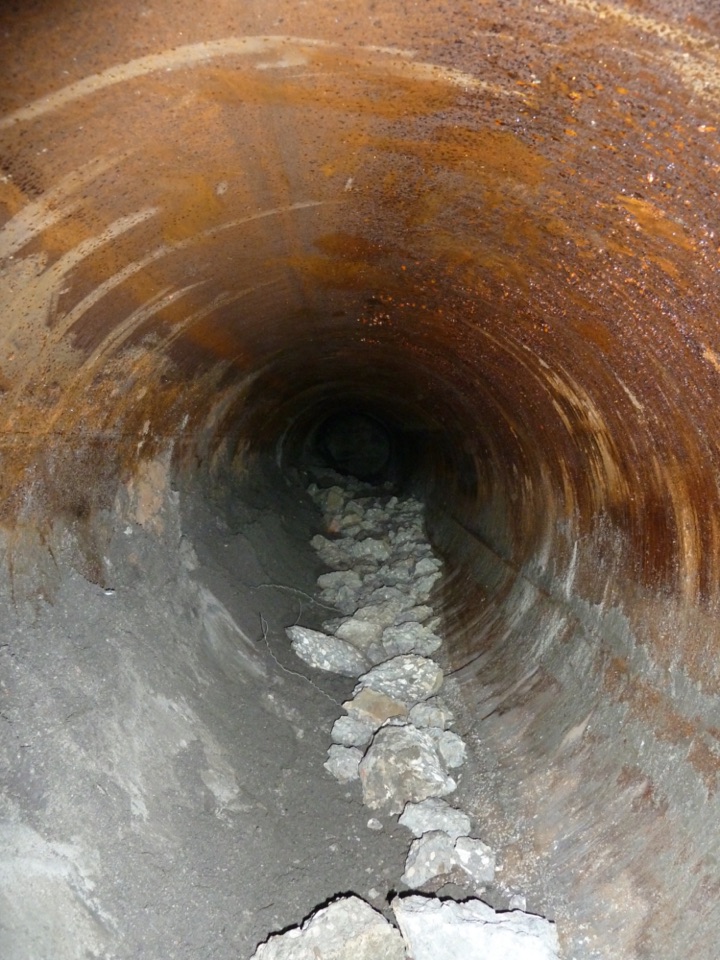
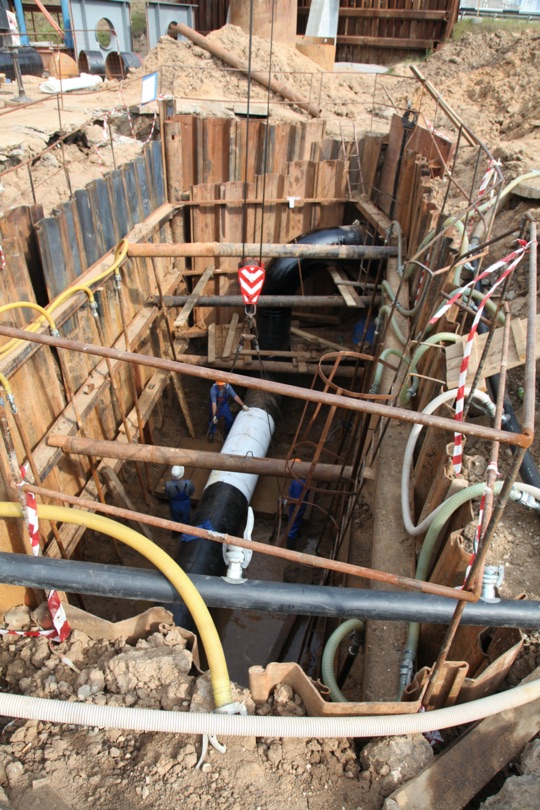